A320 TKE (CAAP)
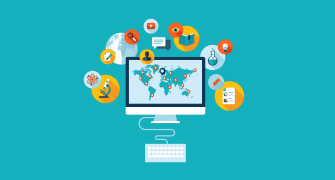
A320 TKE Air Conditioning Quiz
Test your knowledge on the A320's Air Conditioning system with this comprehensive quiz! Designed for aviation enthusiasts, students, and professionals, it covers critical aspects of the air conditioning and avionics ventilation systems.
Prepare yourself for challenges like:
- Detailed multiple-choice questions
- Understanding pack flow and temperature control
- Identifying the roles of key components
Hot air “FAULT” light illuminates on the air conditioning panel:
The hot air press reg. Valve opens and the trim air valves close
The hot air press reg. Valve closes and the trim air valves open
The hot air press reg. Valve closes and the trim air valves close
In case of Air Conditioning System Controller dual lane failure:
No effect. As the other controller will take over.
The related Pack will operate in low flow
The related Pack will operate in high flow
The related Pack is lost, and the hot air pressure regulating valve and associated trim air valves closes.
During normal flight the Avionics Ventilation System controls the temperature of the cooling air by:
Adding air conditioned air to the flow
Extracting air overboard
Adding avionics bay air
Passing air through a skin heat exchanger
The RAM AIR switch should be used:
At any time
Only when delta P is less than 1psi
When press is greater than delta 1psi
Only when outflow valve has fully opened
Air Conditioning System Controller single lane failure:
No effect, as the second lane takes over.
No effect, as the other controller takes over.
Pack is lost
Each Pack is consist of heat exchangers, compressor and turbine. The purpose of the turbine is to:
Expands and cools the air.
Drives the compressor, expands and cools the air.
Drives the compressor, cooling air fan and also expands and cools the air.
The Mixer Unit connects to cabin fans, LP ground connector, emergency ram air inlet, Pack 1 and 2. The statement is:
True
False
Hot air press reg. Valve failed open:
Optimized regulation is lost
The temperature stays at the value selected when the failure occurs
No effect
Bleed air supplied from the APU (APU bleed valve open), the pack flow is automatically selected to:
High
Normal
Low
Trim air valve, each one optimizes the temperature by:
Adding hot air
Adding fresh air
Modulation of pack flow
Hot air pressure regulating valve:
Regulates the pressure of hot air, tapped upstream of the packs
Is springloaded open in the absence of air
Opens automatically in case of duct overheat
Pack flow control valve:
Pneumatically operated and electrically controlled
Electrically operated and pneumatically controlled
Opens automatically during engine starting
The temperature selectors are located in:
The cockpit overhead panel
The cabin stations
Both
Pack flow may be selected from:
The cockpit overhead panel
The cabin stations
Both
Engine flow demand, when the heating or cooling demand in one zone cannot be satisfied:
The minimum idle must be increased manually
The minimum idle is increased automatically
In any case, flight idle is sufficient
What is the maximum norm cabin alt:
8000 ft
9550 ft ± 350 ft
14000 ft
What is the maximum negative differential pressure for the cabin:
0 psi
-1 psi
-2 psi
Is it possible to use simultaneously Packs and LP Ground Unit during long stops in a hot airfield:
Yes
No
Yes, if external temperature is > 50°C
Trim air valves are modulated by:
Air conditioning system controllers
Anti-ice valve
Hot air pressure regulating valve
The mixing unit is connected to:
Packs, cabin air, emergency ram air inlet and LP ground connector
Packs, emergency ram air inlet and LP ground connector
Packs and cabin air
Once set to “ON” the air conditioning packs operate:
Automatically and independently of each other
Normally and dependently of each other
Automatically, pack 1 as a master, pack 2 as a slave
Emergency ram air inlet, when set to “ON”, the ram air valve will open:
In any case
Provided the Ditching pb is not selected
When delta P < 1 psi and the Ditching pb is not selected
Hot-Air Pressure-Regulating Valve is controlled by the:
Air Conditioning System Controller 1
Air Conditioning System Controller 2
Air conditioning System Controller 1 and 2
Conditioned air is distributed to:
Cockpit, cargo bays, and cabin
Cockpit, forward and aft cabins
Cockpit, avionics bay, cabin
The cabin zone temperature sensors are ventilated by the air extracted by the lavatory and galleys fans:
True
False
Temperature control is automatic and is regulated by:
Air conditioning system controllers
Trim air valves
Pack 1 and 2 controllers
The Hot-Air Pressure-Regulating Valve closes automatically when;
Both lanes of the Air Conditioning System Controller 1 fails
Both lanes of the Air Conditioning System Controller 2 fails
Either a or b is correct
The Hot-Air Pressure-Regulating Valve closes automatically when;
There is a duct overheat or pack overheat
Cockpit trim air valve or cabin trim air valves fail
Either a and b is correct
When the pack flow control selector is positioned to HI, air flow is:
80 % of normal
150% of normal
120% of normal
When using APU bleed to supply the Packs, with the Pack Flow Selector at LO, the Pack air flow is:
80% of normal
Normal
120% of normal
The pack flow control valve closes automatically in case of:
Pack overheat, engine fire push button released, engine start, ditching pb pressed
Bleed valve failure, pack outlet pressure increase
Both a and b
Trim air valve failure
The optimized temperature regulation of the corresponding zone is lost.
The optimized temperature regulation of the corresponding zone is still available.
All zones are controlled to 24°C
There are how many trim air valves?
2 - one for the cockpit and one for the cabin
3 - one for the cockpit and two for the cabin
4 - two for the cockpit and two for the cabin
During landing run, packs ram air inlet flaps open when the speed is less than:
77 kts ( after 30 sec delay )
70 kts ( after 3 minutes )
70 kts ( after 20 sec delay )
When APU is supplying the Packs, the air conditioning system controller sends a demand signal to increase air flow when a zone temperature cannot be satisfied:
To the pack ram air inlet flap
To the APU ECB
Pack flow control valve
The ditching switch when selected ON sends a closure signal to:
Outflow valve
Ram air inlet and ventilation inlet extract valves
The pack flow control valves
All of the above
In flight, with cabin pressure controller 1 in use, if it fails:
You have to use the manual control
Transfers automatically to cabin pressure controller 2
You have to select manually to cabin pressure controller 2
You have to set the landing elevation
In normal operation, pressurization is:
Fully automatic
Manually controlled
Both a and b
The outflow valve is powered by:
One of two electric motors
One of three electric motors
Three mechanically linked electric motors
During ground function operation, the outflow valve is:
Fully opened
Fully closed
Positioned according to FMGS demands
To see the position of the outflow valve, it is necessary to call ECAM:
COND Page
BLEED Page
CAB PRESS Page
Two identical, independent, automatic digital pressurization controllers are used for system control:
One controller active, one in standby
Both controllers monitored by FMGC
No controller for climb phase and N°2 controller in cruise and descent
Which controller generates excess cabin altitude and pressure outputs for ECAM indication in manual mode:
Both
N°1
N°2
When Ram Air pb is set to ON, the outflow valve will open 50% when delta P is:
> 1.5 psi
< 3 psi
< 1 psi
The purpose of the safety valves is to avoid:
Excessive positive pressure differential
Excessive negative pressure differential
Both a and b above
The safety valves are operated:
Electrically
Hydraulically
Pneumatically
When landing elevation is set to AUTO, the landing elevation is sent to the controller from:
FMGC
FCU
ADIRS
When Mode SEL is set to MANUAL, the outflow valve is controlled by signals sent via controller 1 or 2:
True
False
On ECAM CAB PRESS page, the outflow valve indicator changes to amber if:
Fully closed
Valve open (more than 95% during flight)
Fully open on ground
On ECAM CAB PRESS page, the safety valve indication changes to amber if:
Both safety valves are fully open
One safety valve is open
Both safety valves are fully closed
On ECAM CAB PRESS page the cabin altitude indication changes to red, when the cabin altitude is:
> 14, 000 ft
> 8, 500 ft
> 9, 550 ft
Following a SYS 1 fault:
Master Caution is activated and ECAM actions must be taken by the crew.
System 2 must be selected by the crew
System 2 takes over automatically without crew action
Cabin pressurization starts at:
Engine start
Take-off power selection
Lift-off
The safety valves open at:
8.06 psi
8.6 psi
9.0 psi
7.6 psi
In automatic mode, cabin pressurization is optimized by using information from:
FMGS landing field elev, dest. QNH and static pressure information
Actual cruise level, cruise N1 setting and landing elevation input
Selected cabin altitude rotary switch and FMGS landing elevation
During normal flight and with skin temp. below + 35 °C, the avionics ventilation system controls the temperature of the cooling air by:
Adding air from the cockpit
Passing air through a skin heat exchanger
Adding conditioned air to the flow
Extracting air from overboard
When the Ram Air pb set to “ON” the emer. Ram air inlet valve will open:
In any case
When ∆P < 1 psi and ditching is not selected
When P < 1 psi and ditching is not selected
The Residual Pressure Control Unit (RPCU) automatically depressurized the aircraft in case of abnormal residual pressure, it automatically opens the outflow valve when:
The OFV is not fully open + both CPCs fail + a/c on ground + all engines shutdown
The OFV is not fully open + both CPCs fail + a/c in flight + all engines shutdown
The OFV is not fully open + both CPCs fail + a/c on ground + all engines running
When the RAM AIR pb is set to ON the outflow valve:
Closes
Opens each time
Opens about 50% only when delta P is less than 1psi
Opens when delta P is greater than 1psi
When the APU master switch is released, a normal APU shutdown occurs:
A.without delay, in all cases
B.with a delay, in all cases
C.with a delay if the bleed air was in use
B and c are correct
What are the APU manual shut down possibilities in the cockpit?
APU master switch pb, APU fire pb switch
APU master switch pb
APU fire pb switch, APU shut off pb
Normal electrical system being available, you may restart the APU up to:
31, 000 ft
20, 000 ft
41, 000 ft
When the APU is running, the APU fuel pump:
Runs when tank pumps pressure is not sufficient
Runs all the time
Runs only in flight
Runs when the APU fuel pump is selected ON
Normal APU rotation speed (N%) is:
100%
Steady at 99%
Steady at101%
APU Master Switch selected ON:
ON illuminates blue. APU system is supplied and APU starts at 95%, AVAIL comes on.
ON illuminates blue. APU system is supplied. APU starts as soon as start pb is depressed and intake flap completely open
APU bleed air is controlled:
By ECB
Not controlled
By APU bleed valve which operates as shut off valve
APU N indication becomes amber on ECAM SD, when:
N ≥107%
N ≥102%
N ≥ 99%
APU EGT indication becomes RED on ECAM SD, when:
A. EGT ≥ 1090°C and 675°C (start and running)
B. EGT ≥ 982°C and 700°C-742°C (start and running)
A and b are correct
On Ground, APU provides:
Electric power + hydraulic power
Electric power + bleed air
Air bleed extraction for Wing Anti-Ice:
Is permitted
Is not permitted
Can you start the APU using the A/C batteries:
Yes
No
The APU is supplied from the:
Left fuel feed line
Right fuel feed line
If Air bleed was used, after a manual shut down sequence the APU:
Stops immediately
Keeps running for four minutes
Keeps running for a cooling period of 60 sec.
AVAIL light illuminates on the Start pb when:
External power is disconnected
APU N reaches above 99.5% or 2 sec after N reaches 95%
APU electric power is used
The APU has its own lubrication system:
Yes
No
What determines the APU speed in accordance with air bleed demand:
Electronic control box
Air conditioning system
Air intake system
Besides the master switch on the cockpit APU panel, APU shutdown is possible by:
A. Switching off the left fuel pump
B. Pushing the APU fire push button
C. pressing APU shut off pb on external Interphone Panel under the nose fuselage
Either b or c
The supply of electrical power has priority over bleed air supply:
No
Yes
Sometimes
Master switch ON, the:
APU starts
ECB is electrically supplied
Air intake flap closes
On ground normal APU rotation speed (N%) without air conditioning is:
100%
Steady at 99%
Steady at 101%
If RMP 2 fails:
The whole system is inoperative
VHF2 and HF2 frequencies cannot be controlled
All COM systems can be controlled by any other RMP
Only VHF2 frequencies cannot be controlled
In normal operation, RMP1 is dedicated to:
HF1 and HF2
VHF1
VHF2
HF1
If you select VHF2 on RMP1, the SEL light illuminates on:
RMP1 and RMP2
RMP1, RMP2 and RMP3
RMP1 only
RMP2 only
To activate the voice recorder before engine start you have to press:
The CVR erase pb
The Ground Control pb
The CVR test pb
You push MECH transmission key on the ACP panel:
You can speak to ground mech through the handset
You can speak to ground mech via ACP INT pb
You are on line with ground mech via ACP CAB pb
You want to erase the CVR recording:
You push the erase pb one time
You push the erase pb for 2 seconds in flight
You push the erase pb more than 2 seconds and check that parking brake is ON
Interphone system permits you to speak to:
The cabin attendants
All occupants in the cockpit
The mechanic on the ground
All the above
Can you obtain an amplitude modulation “A M ” green light on RMP2:
Yes
No
How do you receive ATIS information using the VOR?
Selecting ON VOICE pb on the ACP and VOR reception knob
Selecting ON VOICE pb only
How do you cancel ON VOICE green light?
By depressing again the ON VOICE pb
By depressing the VOR reception pb
Both
What is the function of the RESET pb on the ACP?
To restart system operation
To cancel the previous selections
To cancel any lighted calls
When using the OXY Mask or Boom headset, if the INT/RAD key is set to INT. Will interphone background noise be heard when using the sidestick PTT for radio transmissions?
Yes
No
You make a STBY/NAV selection on a pedestal RMP. Can you confirm that selection on MCDU-RAD/NAV page:
Yes
No
Is STBY/NAV tuning possible on RMP-3
Yes
No
Can you hear the beacon identification selected through the STBY/NAV:
Yes, by pressing corresponding reception knob
Yes, by pressing a LSK on the MCDU
Can you hear the Voice Recorder test signal through the cockpit loud speakers, with the parking brake released:
Yes
No
You receive a SELCAL on VHF2, What happens on your ACP:
Amber sign CALL flashes on VHF2 key
Three green bars come on
White SELCAL appears on VHF2 pb and VHF2 reception selector illuminates white
Can you speak on VHF and the PA at the same time:
Never
Yes by pressing RAD toggle sw and PA key
Yes by using stick PTT command and PA key
When you select CAPT 3 on the audio switching panel:
The captain uses headset of 3rd occupant
3rd occupant uses captain equipment
The captain uses his acoustic equipment and the 3rd occupant ACP
Can you select VOR 2 frequency with RMP1?
Yes
No
If VHF 1 is selected on RMP 2, SEL light illuminates white:
On RMP 2
On RMP 1
On RMP 1 and 2
If RMP 1 fails the crew can only use RMP2:
By switching off RMP 1, then using RMP 2
By using overhead panel audio switching: CAPT 3
In case of dual FMGC failure, selection of radio navigation frequencies is possible with:
RMP 1 only
RMP 1 and 2 only
RMP 1, 2 and 3
For communication with ground mechanic at the engine nacelle, the crew must use the following audio system selection:
Mech + INT
ATT + CAB
Any of the above
Cockpit Voice Recorder is energized, on ground as soon as aircraft electrical network is supplied but only for 5 minutes. It starts again as soon as:
GND CTL is on
One engine is running
A or b
If an RMP fails, the selected receiver is no longer controlled by this RMP and frequencies and bars disappear from this RMP:
Yes
No
What is the main purpose of the RMP:
To select radio frequencies
To select NAV AIDS when the FMGS has failed
Both
Can you use service Interphone system in flight:
Yes
No
If ATC mode selector at AUTO:
Selected ATC operates only in flight
Selected ATC operates when FLEX or TOGA power is selected for T.O
Selected ATC operates as soon as one engine is running
On ATC control panel the ATC FAIL light comes on if:
Selected transponder fails
System 1or 2 has failed
On RMP, the ON/OFF switch controls:
The power supply to the RMP
Only the STBY NAV function of RMP
Only the COM functions of RMP
STBY NAV has been selected by the use of NAV key:
VHF function is lost on this RMP
VHF is still available but only the last frequency selected can be used
NAV key has no effect on Radio COM frequency selection
In normal configuration, How is DC ESS BUS supplied?
From TR1
From ESS TR
From TR 2
From Bat 2
What happens in case of total loss of main generators?
The RAT is automatically extended and powers the yellow system which drives the emergency generator
The RAT is automatically extended and powers the blue system which drives the emergency generators
The RAT has to be manually extended
The RAT extended and mechanically connected to the emergency generator
AC ESS Bus is normally supplied by?
AC BUS 1
AC BUS 2
Emergency Generator
Static Inverter
DC BAT BUS can be supplied by:
DC bus 1 or batteries
DC bus 1, DC bus 2 or batteries
DC bus 2 or batteries
AC BUS TIE contactors enable the electrical system:
To be connected in a parallel
To be supplied by any generator or external power
To be supplied by APU GEN or EXT PWR only
What happens during the EMER GEN test?
The ram air turbine (RAT) is extended
If the blue system is pressurized, the emergency generator comes on line
The green system is pressurized and the emergency generator comes on line supplied by hot bus 2
Normal minimum battery voltage before APU start is:
22 V
25.5 V
27.5 V
No minimum
When disconnecting the IDG, the button should be pressed:
For no more than 3 secs.
For longer than 3 secs.
Until fault light goes out
For no more than 5 secs.
On the EMER ELEC PWR panel, a red FAULT light illuminates under the “RAT and EMER GEN” label. What does it mean?
RAT is not extended
Emergency generator is not supplying when AC bus 1 and 2 are not powered (above 100 kts) or DC bat bus is not powered
Emergency generator is supplying but AC ESS bus is not powered
Emergency generator is not supplying when AC bus 1 and 2 are not powered
What happens when the GEN 1 LINE pb is set to OFF?
AC BUS 1 and 2 are not powered and emergency generator is automatically connected
AC BUS 1 is powered by the GEN 2 because the GEN 1 is deactivated
AC BUS 1 is powered by the GEN 2 because the GEN 1 line contactor is opened
AC BUS 1 is not powered because the GEN 1 line contactor is opened and transfer contactor is not closed.
In cold aircraft configuration (no AC and no DC supply), where the batteries voltage can be checked?
On the ECAM ELEC page
On the ELEC overhead panel
There is no indication
AC ESS BUS is normally supplied by:
AC BUS 1
AC BUS 2
Static inventer
IN flight, On Batteries Only, the AC ESS SHED BUS and the DC ESS SHED BUS are lost:
Yes
No
The static inventer works:
Always
When A/C is in flight and on batteries only
When one main generators fails
On ground, what happens when the “RAT and EMER GEN MAN ON P/B” is pressed in:
The RAT is extended
The emergency generator is activated
The static inverter transforms the DC voltage from the battery bus into:
Single phase 115 V – 400 HZ AC current
Three phase 115/200 V – 400 HZ AC current
In flight, in case of loss of all main generators, emergency generator not running, the static inverter supplies:
APU and ENG start + AC ESS bus
ENG start + AC ESS + AC ESS shed bus
ENG start
The external power has priority over the APU GEN:
Yes
No
GEN 1 and GEN 2, when operating, have priority over APU GEN:
Yes
No
With APU available, if one generator fails, the failed generator is replaced by:
The APU
The other GENERATOR
The ESS TR may be used to replace a faulty TR:
Yes
No
In flight, in case of loss of all generators, emergency generator not running, the DC ESS bus is supplied by:
BAT 2
ESS TR
Both
In flight, in case of loss of all main generators, emergency generator running, the DC ESS BUS is supplied by:
Hot bus
ESS TR
Both
The IDG regulates the generator:
Speed
Voltage
Frequency
Generators are sometimes connected in parallel:
Yes
No
If AC bus 1 fails the AC ESS BUS is supplied by the:
EMER GEN
AC bus 2
Static inverter
In case of total electrical loss the AC ESS BUS is supplied by:
Static inverter
EMER GEN
Both
In emergency configuration, AC ESS SHED BUS is automatically:
Shed if the RAT stalls
Supplied by static inverter when L/G is down
Only one generator is operating in flight:
Main galley is automatically shed
Secondary galley is automatically shed
All galleys are shed
Can you reconnect the IDG in flight?
Yes
No
When GEN 1 or GEN 2 is selected off:
The GEN is deenergized and line contactor is open
The GEN is still energized and line contactor is open
When the EXT PWR pb green AVAIL lite is illuminated, this means that:
The EXT PWR is connected to the A/C
The A/C network is supplied
When are the batteries supplying the DC BAT BUS:
A. APU starting
B. Loss of AC bus 1
C. Loss of AC bus 1+2 (speed < 100 kts)
A + c
When you want to check battery voltage, you must set the BAT pb to:
Auto position
Off position
The battery FAULT light illuminates when:
Battery voltage < 25V
Battery pb set at OFF in flight
Charging current increases at an abnormal rate
In certain cases, the static inverter is supplied by:
BAT 1 and BAT 2
BAT 1
DC BAT BUS
BUS TIE contactors when closed enable AC BUS 1 and 2:
To be supplied by anyone of the main generators or external power
To be supplied by APU generator or external power only
To be connected in prallel
In case of the TR (1 or 2) failure, does the ESS TR supply the DC ESS BUS:
Yes
No
The green EXT PWR pb AVAIL light is ON what does it mean?
The EXT power is plugged in, and parameters are normal
The A/C network is supplied
What additional external warnings are activated in case of an APU fire on ground only?
APU fire light accompanied by an external horn warning
An external horn warning
A fire bell warning
Where are the engine fire detectors located?
On the fan and the turbine
On the pylon, the fan and the core
On the core and the gearbox
The agent pushbutton is active when?
The corresponding “DISCH” light is on
Engine fire pb illuminates
Engine fire pb is pressed and released
What does the TEST pb verify?
The detection system loop circuit integrity
The squib circuits of the extinguishing system
Both
The Engine and APU fire protection system includes:
1 fire agent bottle for each engine – 1 fire agent bottle for the APU
2 fire agent bottles for the engine – 2 fire agent bottles for the APU
2 fire agent bottles for each engine – 1 fire agent bottle for the APU
Is the extinguishing system controlled by the FDU:
Yes
No
When Engine Fire pb is released out which corresponding valves are closed:
Fuel crossfeed valve
LP fuel and hydraulic fire valves
HP fuel SOV
How is an APU fire on ground normally extinguished:
From APU fire panel
Automatically
From external power panel
How can a thermal discharge of the APU fire bottle be detected when no electrical power is connected:
By the FDU
By the ECAM
By the red disc indicator missing
How many fire detection loops does the APU fire detection system comprise:
Three
Two
One
What systems are isolated when APU fire push button is released out:
Fuel, electricity
Air, electricity
Fuel, air, electricity
When Engine Fire pb is released out, which valve is affected:
LP fuel is shut off valve, Hyd, Bleed, Pack + Elec Gen relay will de-energize.
Hydraulic fire shut off valve
Fuel SOV
When the APU Fire pb is released out, the:
APU generator is de-energized
APU generator is disconnected
APU generator is energized
Is it necessary to use the APU shut off switch on the external power panel in case of APU fire auto extinguishing on ground:
Yes
No
When the ENG Fire pb is released out, what aircraft systems are isolated:
Fuel, electricity, air
Fuel, hydraulic, air
Fuel, air, electricity, hydraulic
When an ENG Fire pb is released out, the squib light are illuminated:
Yes
No
Which systems are tested through the Fire test pb?
The fire detection system
The extinguishing system
Both
The pitch direct law is:
A load factor demand with no protection
A direct side stick to elevator relationship
A direct side stick to elevator relationship with AUTOTRIM operation
Achieved through the THS using manual trim control
When is the THS not available?
After blue hydraulic system failure
After yellow and green failure
Never lost, always available manually
After loss of FAC 1 and 2
The PFD displays in amber the message “USE MAN PITCH TRIM” in
Normal Law
Alternate Law
Direct Law
Which surfaces are used for lift dumping?
All spoilers
Spoilers 1 to 3
Spoilers 1 to 4
Which signals cause rudder pedal movement?
Yaw damping signals
Rudder trim signals
Turn coordination signals
If ELAC 1 and 2 have failed:
Pitch control is provided by the FAC's
Pitch control can only be achieved from the trim wheel
The elevator and pitch trim are controlled by SEC 1 or 2
If FAC 1 and 2 have failed:
The rudder can always be controlled from the pedals
The rudder control is lost
The rudder control is provided by SEC 3
When both sticks are moved in the same or opposite direction:
The surface movement is proportional to the algebraic sum of the deflections of both sticks
The surface movement is proportional to the last stick deflected
The surface movement is proportional to the first stick deflected
The left stick has a priority
The elevator, ailerons, spoilers are:
Hydraulically activated and mechanically controlled
Electrically activated and hydraulically controlled
Hydraulically activated and electrically controlled
Rudder control is electrical for yaw damping and trim:
Yes
No
What statement is correct:
Ground spoiler function: all spoilers deploy
Speed brake function: spoilers 1, 2, 3 deploy
Roll function: ailerons + spoilers 4 and 5 deploy
How many control modes are there on the elevators servo jacks?
2 - active and damping
3 - active, damping and centering
4 - active, semi-active, damping and centering
What are the limits for maneuvre protection:
A. +2.5 G, -1 G clean
B. +2.0 G, -0 G when Flaps extended
A and b are correct
Which ELAC normally controls the elevators and the stabilizer:
ELAC 1
ELAC 2
How many hydraulic motors drive the screw jack of the stabilizer:
2
3
How many electric motors can control the hydraulic motor of the stabilizer:
1
2
3
If neither ELAC 1 nor ELAC 2 are available, pitch control is automatically transferred to:
SEC 1 or SEC 2
SEC 1 or SEC3
Sec 3
In normal law, the flight mode changes to the landing mode when passing:
50 ft
100 ft
At landing when passing 30 ft:
The altitude is memorized
The altitude is progressively reduced to 2º nose down over a period of 8 secs.
How can a deactivated stick be reactivated:
By momentary action on take over push button of the active stick
By momentary action on either stick take over push buttons
By momentary action on take over push button of deactivated stick
In roll normal law, the bank angle protection is active when bank angle is:
> 45 degrees
> 33 degrees
> 67 degrees
The roll normal law provides combined control of the:
Ailerons + spoilers 2 to 5 + rudder
Ailerons + spoilers 2 to 5
If ELAC 1 and ELAC 2 have failed:
Roll control is provided by ailerons only
Roll control is provided by ailerons and spoilers
Roll control is provided by spoilers only
In flight, if a WTB (wing tip brake) is activated, can you release it:
Yes
No
What happens when SFCC 1 fails:
Nothing
Flaps and slats operate at half speed
Flaps system lost
If one Flap power control unit fails, what happens:
Nothing
Flaps at half speed
Flaps are lost
If CONF. 0 is not selected after take-off, the flaps automatically retract at:
>180 kts
210 kts
V2
After an automatic retraction of the flaps with CONF. 1, the flaps will automatically re-extend when speed decreases:
Yes
No
Is it possible to select an intermediate position with the flaps and slats selector:
Yes
No
If you are flying at an angle of attack more than Alpha Prot, what happens when you release the stick:
Speed returns to VLS
Speed returns to Alpha Prot
When ALT LAW is active, the High Speed and High Angle of Attack protections are:
Degraded
Lost
When ALT LAW is active, the Yaw Damping is:
Available (damper authority is limited to ±5 degrees of rudder deflection)
Lost
When in CONF 1+F, the flaps retract to 0º automatically at 210 kts:
Alpha/Speed Lock function
Automatic Retraction function
Flap Load Relief function
How many hydraulic systems activate the rudder:
1
2
3
Lift augmentation is achieved on each wing by:
3 flap surfaces + 4 slat surfaces
2 flap surfaces + 5 slat surfaces
Slat retraction from 1 to 0 is inhibited if angle of attack exceeds 8.5º or speed goes down below 148 KTS, this function is called:
Alpha/Speed Lock
Automatic Retraction System (ARS)
Flap Load Relief System (FLRS)
In alternate law, the change to direct law occurs when:
Landing gear down or at the selection of flaps 2 (LGCIU 1 + 2 fault)
Landing gear down
Passing 50 ft
Slats SYS 1 fault on the ECAM warning display means:
SFCC 1 has failed
The slat channel in one SFCC has failed
With hydraulic blue system remaining and before landing gear extension, the flight control law is:
Alternate
Normal
Direct
In flight control normal law, the stall warning is activated:
If slats are not extended when reaching a speed of 148 knots
When Alpha Max is reached
When Alpha Prot is reached
Angle of attack corresponding to stall warning cannot be reached in normal law
The pitch normal law provides:
Manoeuvre protection + pitch attitude protection + high speed protection
Manoeuvre protection + high angle of attack protection + high speed protection
Manoeuvre + high angle of attack + high speed + pitch attitude protection
Manoeuvre protection + pitch attitude protection + low speed stability
When is the THS not available?
After yellow and green hydraulic system failure
Never lost, always available manually
After blue hydraulic system failure
After loss of FAC 1 and 2
Flight control computers are:
2 ELACs - 2 SECs - 3 FACs
2 ELACs - 3 SECs - 2 FACs
3 ELACs - 2 SECs - 2 FACs
When bank angle protection is active, is auto trim is inoperative?
Yes
No
What does it mean when the ADR fault light illuminates steady on then ADIRS CDU?
A fault is detected in air data reference
No present position entry after 10 min.
Alignment has been completed
On the pedestal mounted switching panel, the ATT HDG and Air Data selectors are at NORM, meaning:
ADIRU 1 supplies data to PFD1, ND1 / ADIRU 2 supplies data to PFD2, ND2
ADIRU 1 supplies data to PFD1, ND1 and DDRMI / ADIRU 2 supplies data to PFD2, ND2
ADIRU 1 supplies data to PFD1 / ADIRU 2 supplies data to PFD2
Tuning of VOR/DME and ILS is provided by:
Automatic tuning, Manual tuning, Back up tuning
Automatic tuning Manual tuning
Automatic tuning Back up tuning
In case of failure of FMGC 1 and 2:
VOR, ILS and ADF receivers 1 and 2 can be tuned through RMP1
VOR, ILS and ADF receivers 1 can be tuned through RMP1
RMP1 controls VOR, ILS DME and ADF receivers 1 / RMP2 controls VOR, ILS DME and ADF receivers 2
The ALIGN light flashes:
Within five minutes of NAV mode selection when present position has not been entered
During the alignment phase in case of IRS alignment fault
When alignment has been completed
The FMGS consist of the following main components:
2 FMGS – 2 MCDU – 2 FAC – 2 FCU control panels
2 FMGS – 2 MCDU – 2 FAC – 1 FCU control panel
2 FMGS – 2 MCDU – 2 FAC – 2 ECAM
2 FMGS – 2 MCDU – 2 ECAM – 1 FCU control panel
Normal electrical power supplies the A/C and the MCDU CRT is dark, without any other warning. It means:
The FMGC is off
The FMGC has failed
The MCDU CB is pulled
The MCDU “BRT” knob is dimmed
On the ground, when electrical power is initially supplied to the A/C, the MCDU will automatically display:
Airport page
INIT A page
Data Index page
A/C Status page
You press “ALIGN IRS” prompt on INIT A page. On the ADIRS CDU the ALIGN lights flash but no message is displayed on the CDU:
The system can only be used in ATT mode
The system is unable to enter NAV mode to compute coordinates: switch it off
Make a second “present position” entry
These messages appear on copilot side ND: “SET OFFSIDE RNG/MODE” & “MAP NOT AVAIL”:
The IRS's have not reached complete alignment
The F-PLN entered in captain's FMGC has not been transferred into copilot's FMGC
Single FMGC operation and the two EFIS control panels are not set at the same range & mode
Engines running, ready to taxi, a message appears: “CHECK GW”. Access to INIT B page is no longer available. On which page is it possible to insert the correct GW:
T/O performance page
Progress page
Fuel prediction page
Aircraft on RWY centerline, ready for take-off. To preset a HDG of 233 degrees:
Pull HDG knob to disarm NAV mode Set 233 degree and press HDG knob to engage
Turn HDG knob, set 233 degree and pull to engage
Turn HDG knob, set 233 degree, Pull HDG knob when ATC clears to turn to 233 degree
One of the SRS disengagement conditions is not true:
Disengages automatically at FCU alt
Disengages automatically at acceleration altitude
Disengages manually by pulling the speed knob
Disengages by setting a new FCU altitude
Control of the A/C can be automatic or manual. Guidance of the A/C can be managed or selected. How do you understand this situation. Managed guidance – manual control – selected speed:
FMGC computes and sends steering orders for navigation purpose. The pilot flies through the sidestick. Speed is adjusted in the FCU window.
The audio pilot follows the F – PLN. The pilots set the necessary data for longitudinal and lateral control of the A/C. The target speed is computed and displayed by the FMGC
A hold has been entered in the F-PLN, speed and NAV are managed. You want to leave this hold:
Use the CLR key
Hold is automatically cancelled when overflying the fix
Activate IMM “EXIT*” prompt
For A/C position determination, FMGC uses data from:
A. DME, VOR or ILS systems
B. Clocks + Ground Speed Computation
C. 3 ADIRS
A. And c.
In flight, following a manual position up-dating of the FMGC:
It is also necessary to up-date the IRS position
An IRS cannot be up-dated during A/C motion
The Expedite mode is active. To disengage it, one of these statements is not correct:
Pull the V/S – FPA knob
Pull the SPD knob
Pull the ALT knob
Press again the EXPD PB to cancel this mode
What are the basic modes of the AP/FD:
Pitch and Roll
HDG and VS
ALT and NAV
SPD and HDG
The engagement of both autopilots is possible:
When “LAND” illuminates green on FMA
When A/C is stabilized at G/S interception altitude
As soon as the LOC has been intercepted
After APPR pb switch is pressed and illuminates
Can you read the HDG on the PFD:
Yes
No
A/C is in clean configuration and in Normal Law. When the FAC detects a too high angle of attack:
Stall warning is activated
THR LK flashes on FMA
Alpha floor function operates
During ILS approach, LAND 3 Fail Passive (also called CAT 3 single), one engine fails below 100 feet RA: This causes a landing capability down grading and you must go around:
True
False
During an ILS approach the NAV mode will be deactivated at:
A. Glide Slope capture
B. Localizer capture
A. + b.
Can you display FD bars and FPV at the same time, for cross-checking on different PFDs;
Yes
No
Certified FMGS limitations. Max wind conditions for CAT III automatic approach performed in managed speed guidance with A/THR: Head wind Tail wind Cross wind
A. 30 KT 10 KT 20 KT
B. 40 KT 10 KT 15 KT
C. 20 KT 10 KT 20 KT
The continuous cavalry charge audio identifies only one of the following situations:
Over speed for the actual A/C configuration
Fire or oil low press on one engine
Autopilot Disengagement
Excessive cabin altitude
Auto land warning, requiring a Go Around
Setting the thrust levers at idle will disengage the A/THR mode. A/THR will reengage:
As soon as the thrust levers position is changed
When A/THR pb is pressed on the FCU
Provided the levers are set in CLB gate
Provided the levers are moved from idle position and A/THR pb is pressed
In one of the cases listed below, A/THR does not disengage:
When the two thrust levers are set at idle position
Pressing the A/THR pb on the FCU
When the aural warning announces “RETARD!”
Pressing the instinctive disconnect button
The LOC pb, on the FCU, is pressed to ARM LOC mode. This mode is used for:
A. Performing a published localizer approach
B. Tracking a VOR beam during an approach
C. Performing those non-precision approaches: VOR-ADF-R NAV
D. Approaching on an ILS with no G/S
A and d
What does a triple click mean, during an ILS approach:
A level 3 warning to the crew
A primary failure is occurring, prepare for Go Around
Flaps are set at 3 and the landing gear is not down
Landing capability down grading warning
The active F-PLN is erased when:
The pilot calls the A/C status page
The wheels touch the runway at landing
The A/C has been on ground for 30 seconds following the landing
One engine is shut down at parking place
Following a dual engine generator failure, EMER GEN supplies the A/C:
FMGC 1 is available (NAV function only)
FMGC 2 only is available
Both FMGCs are available
No FMGC is available
In which case are: AP/FD, ATS and Landing Capacities totally lost:
2 IRSs failure or 2 ADRs failure
2 RAs failure
2 ILSs failure
Both FACS failure
The mandatory parameter used by the alpha floor detection is:
A/C minimum speed
A/C weight
A/C maximum speed
A/C angle attack
Rudder travel limitation is a function of:
FAC only
FAC in normal and ELAC in alternate
ELAC only
ELAC in normal and FAC in alternate
When the two YAW damper functions are engaged:
YAW damper 1 has priority, YAW damper actuator 2 is slaved
YAW damper 2 has priority, YAW damper actuator 1 is slaved
YAW damper 1 and 2 are active, the two actuators pressurized
A hydraulic device gives priority to YAW damper 1
The safety tests are automatically performed:
On ground, at computer power up
In case of discrepancy between 2 computers
In flight when a failure occurs
In flight at autopilot engagement
When the two rudder trim functions are engaged:
Rudder trim 1 and 2 control their motors together
Rudder trim 1 controls the single trim motors
Rudder trim 1 controls its motor, rudder trim 2 is in standby
A mechanical device gives priority to rudder trim 1
The FMGC functions are:
Flight guidance and flight envelope protection
Flight management and flight envelope protection
Flight management and flight guidance
Flight envelope protection and yaw axis control
The trim function of the FAC is:
A Pitch Trim
A Rudder Trim
An Aileron Trim
A Pitch Trim and Rudder Trim
In flight, in case of temporary loss of electrical power on FAC 2, FAC 2 pb “FAULT” comes on and:
It will be automatically reset
It can be manually reset and the safety tests are performed
It can be manually reset and the safety tests are not performed
There is no way to reengage FAC 2
The AFS computers are:
FMGC and ELAC
FMGC and SEC
FMGC and FAC
ELAC and SEC
With AP1 and AP2 not engaged, FD1 and FD2 engaged and A/THR active:
FMGC1 controls engine 1, FMGC 2 controls engine 2
FMGC1 control both engines
FMGC2 controls both engines
Flight controls and engines are controlled by only one FMGC
The autopilot does not disengaged in case of override on: (in flight)
The sidestick in roll
The sidestick in pitch
The rudder pedals
A rudder pedal deflection less than 10° out of trim
In normal operation, with the two MCDU showing the same page, a modification made by the pilot on MCDU 1 is sent to MCDU 2:
Directly
Via FMGC 1
Via FMGC 1 and FMGC 2
Via FMGC 1, FMGC 2 and RMP 2
The flight guidance function are:
Autopilot, Flight plan, Autothrust
Autopilot, Performance, Flight plan
Autopilot, Flight director, Autothrust
Flight Management, Autopilot, Autothrust
The position of the aircraft, used in the flight plan is computed by:
FG part of the FMGC
FM part of the FMGC
The DMC
The MCDU
The flight director is engaged:
By pressing the FD pb on the FCU
Automatically at system power up
By selecting a mode on the FCU
By selecting the INIT page on the MCDU
With autopilot engaged, the rudder is normally controlled by:
The FMGC
The FAC
The ELAC
The SEC
The normal FMGC operation is:
Only one FMGC can operate at a time
FMGC 1 has priority, FMGC 2 is in standby
FMGCs operate according to master/slave principle
FMGCs operate independently
The FCU allows:
Modification of the flight plan of FM part
Selection of FG function modes
Selection RADIO-NAV frequencies
IRS alignment
In cruise, lateral AP orders are executed by:
Ailerons and spoilers
Ailerons and rudder
Rudder and spoilers
Ailerons, spoilers and rudder
With the aircraft in flight, AP engaged and A/THR active, the A/THR mode:
Can be chosen by the pilot on the FCU
Can be chosen by the pilot on the MCDU
Depends on the AP lateral mode
Depends on the AP longitudinal mode
With the aircraft in flight, A/THR not engaged, thrust levers on CLB gate, an alpha-floor is detected:
A/THR does not get engaged because the engines are already in CLB thrust
A/THR automatically engages, but is not active
A/THR automatically engages and controls the engines with CLB thrust
A/THR automatically engages and controls the engine with TO/GA thrust
The FAC computes rudder travel limit:
Only when AP is engaged
Only at low speed
Only in case of ELAC failure
At any time
With AP engaged in LAND mode, the YAW damper actuator is controlled by:
A yaw order computed by the FAC
A dutch roll damping order computed by the FAC
A turn coordination order computed by the FAC
An AP yaw order computed by the FMGC, via the FAC
On the FMA, on the second line of the longitudinal zone:
ALT can be only in green or magenta
ALT in cyan indicates that ALT mode is active
ALT in cyan indicates that ALT mode is armed
ALT in cyan indicates that ALT mode is active or an FM altitude constraint
With the thrust levers in the CLB gate, A/THR disengages; the engines thrust:
Equals CLB thrust limit
Is frozen at the existing thrust
Corresponds to the thrust levers position
Progressively becomes equal to the thrust lever position
When TAKE-OFF mode is engaged:
A/THR automatically engages and is active
A/THR automatically engages but is not active
A/THR does not automatically engage and the engines are controlled by the thrust levers
A/THR does not automatically engage and the engines are controlled by the last thrust target
ADIRU 3 can supply information to:
DMC 1 and DMC 2 only
DMC 1 and DMC 3 only
DMC 2 and DMC 3 only
DMC 1, DMC 2 and DMC 3
Air data modules (ADM) supply pressure information to the ADIRUs from:
All pilot probes and static ports
The pilot probes only
The static ports only
The captain and first officer pitot probes and static ports only
ADIRS 3 receives TAT information from:
The captain's TAT sensor
The first officer's TAT sensor
The captain and first officer's TAT sensors
The stand-by TAT sensor
The BARO correction or reference selected is sent to each ADIRU via:
The master FMGC
The FCU
The RMPs
The DMCs
Each ADIRU receives two analogue inputs. They are:
Angle of attack (AOA) and total air temperature (TAT)
Angle of attack (AOA) and barometric correction or reference
Total air temperature (TAT) and barometric correction or reference
FMGC status and barometric correction reference
In normal operation the ADIRUs aligned using information from:
The ADIRS CDU
The CFDS
The FCU
The MCDU
If ADIRU 2 fails, the correct action is:
Set ATT HDG and AIR DATA selectors to CAPT/3
Set ATT HDG and AIR DATA selectors to F/O/3
Set ATT HDG selectors to CAPT/3, AIR DATA selector to F/O/3
Set ATT HDG selectors to F/O/3, AIR DATA selector to CAPT/3
In normal operation ADIRU 1 supplies information to:
The captain's PFD and the first officer's ND
The captain's ND and the first officer's PFD
The captain's PFD and ND
The first officer's PFD and ND
In rose NAV mode with VOR 1 selected, the ND displays what VOR information:
Deviation bar, selected course and the bearing pointer
Bearing pointer only
Deviation bar and selected course only
Deviation bar and bearing pointer only
In ROSE ILS mode, the ND displays what ILS information:
G/S and LOC scales
Deviation bar and selected course
Deviation bar, selected course and G/S scale
Deviation bar, selected course, G/S and LOC scales
In the event of no ADF1 reception, with ADF1 selected on ND:
The bearing pointer goes out of view and ADF flag is displayed
The bearing pointer goes out of view and station ID is replaced by red crosses
The bearing pointer goes red and station ID is replaced by frequency
The bearing pointer goes out of view and station ID is replaced by frequency
In ROSE VOR mode, in the event of VOR receiver failure:
The VOR information and the course pointer becomes red
The VOR information becomes red and the course pointer disappears
The VOR information and the course pointer disappear
The VOR information flashes and the course pointer disappears
During Take-Off and Go Around, the speed window on the FCU displays:
The speed manually inserted by the crew into the FCU and the light is out
The speed manually inserted by the crew into the MCDU and the light is illuminated
Dashes and the light is illuminated: managed speed such as V2 or memorized VAPP are automatically used by the FMGS
The following AP/FD lateral modes are managed:
NAV, HDG, APPR, LOC, RWY, RWY TRK
HDG, NAV, APPR, LOC, GA TRK
NAV, APPR, LOC, RWY, RWY TRK, GA TRK
In approach, “LAND” illuminates green on FMA when radio altitude is:
700 feet
400 feet
1,000 feet
200 feet
On the ground, the engagement of the autothrust function:
Must be carried out manually by the crew before take off
Is performed automatically upon the second engine start
Is performed automatically at the engagement of the take off mode
Climbs and descents are always limited:
By flight plan (T/C) and (T/D) points
By the altitude manually selected on the FCU
By the aircraft weight calculated by the FMGC
In flight, the FMGS position can be updated:
Whenever a DME station is selected by the pilot
Using data from the selected NDB, VOR or DME stations
Automatically with the DMEs through the autotuning function
ON the ND, in the event of VOR receiver failure:
The red VOR flag is displayed, the course pointer disappears
The VOR bearing becomes red and the course pointer disappears
The VOR bearing and the course pointer disappear
The VOR bearing flashes and the course pointer disappears
In flight, the FMGS position is automatically updated:
Using data from the selected NDB, VOR or DME stations
Whenever a DME station is selected by the pilot
By the DMEs through the autotuning function
How many pumps are there in each fuel tank?
One fuel pump each tank
Two fuel pumps in each tank
There is no fuel pump because tanks are air pressurized
Two fuel pumps only for all tanks
Normally, where can you check the fuel quantity of each tank?
On ECAM upper display and on FUEL page
On ECAM lower display FUEL page only
On ECAM upper display
On ECAM upper display, or no refueling control panel
With all fuel pumps switches ON, are wing tank pumps running while center tank is supplying?
Yes, wing tank pumps are always running
No, only when center tank is empty
No, because of center tank pump priority
How many cells in each wing tank?
Two
Three
Where is the vent surge tank located?
In the outer section of each wing
In the wing tank
Where is the fuel remaining in the surge tank scavenged?
Inner cell
Outer cell
Which type of motor controls the fuel cross-feed valve?
Single
Double
Where are the transfer valves located?
In each outer cell
In each inner cell
On each sealed rib of each wing tank
What is the purpose of the pressure relief sequence valves?
Allows the transfer, from wing tanks to center tank
When all pumps are running, center pumps will deliver fuel preferentially
In normal operation, each engine is supplied by:
One wing tank pump and one center tank pump
Two wing tank pumps and two center tank pumps
Two wing tank pumps and one center tank pump
Is the gravity feeding from center tank possible:
Yes
No
The LP valves are controlled to off position by:
Engine master switches
Engine master switches and fire pbs
Fire pbs
The normal tank filling order is:
Wing tanks then center tank
Center tank then wing tanks
Amber FAULT light illuminates on tank pump pb when:
Pump is not energized
Pb at off without failure
The delivery fuel pressure drops
Amber FAULT light illuminates on MODE Sel. Pb when:
The delivery fuel pressure drops
Center tank has more than 250 kg and any wing tank has less than 5000 kg
The two center tank pumps are selected off
The maximum fuel imbalance is (Take Off & Landing) at heavier tank full:
1500 kg
1800 kg
2000 kg
The maximum refueling pressure is:
50 psi (3.5 bars)
36 psi (2.5 bars)
11 psi (0.75 bars)
FOB (Fuel on Board) half-boxed amber on ECAM FUEL page means:
Both transfer valves fail to open when inner cell is at low level
One transfer valve fails to open when inner cell is at low level
FQI (Fuel Quantity Indicator) is degraded
FOB ( Fuel on Board) half-boxed amber on EWD means:
The quantity shown is not fully usable
Fuel quantity indicator is degraded
If open, when will the transfer valves close again?
When the cell is empty
Transfer valves close automatically at the next refueling operation
For what purpose is fuel used by electrical system?
To cool the IDG oil
To cool the engine oil
APU fuel is supplied by:
Engine fuel pump(s) only
APU fuel pump only
Either one
With slats extended, the center tank pumps run on ground:
Always
Never
Yes, after engine start for 2 mins.
What does the MODE SEL pb control:
Center tank and wing tank pumps
Center tank pumps only
Wing tank pumps only
When the center tank is empty (MODE SEL at AUTO), center tank pumps:
Must be manually switched off
Stop automatically and wing tank pumps start running
Stop automatically 5 min. after LO level is reached in center tank
What happens to the IDG cooling fuel when the outer cells are full:
Fuel returns to the engine feeding line
Fuel overflows into the inner cell through a spill pipe
What happens to the IDG cooling fuel when the wing tank is full:
Fuel goes directly into the center tank
Fuel returns to the engine feeding line
The system select CTR TK pumps off. WING TK pumps feed approx. 500 kg, then CTR TK pumps run again
Suction valves are:
Always open regardless of pumps status
Normally closed by pumps pressure
Open automatically when fuel X-feed is selected on
Why has a 2% additional space been provided in each fuel tank?
For cooling purposes
For fuel expansion without spillage into the vent surge tank
During take off, center tank fuel is:
Supplying to both engines
Not supplied while slats are extended
Not supplied with the MODE SEL at AUTO
Required to be deselected by the pilot
With fuel in all tanks, in flight, fuel is used:
From the inner cells and outer cells then the center tank
From the outer cells and inner cells then the center tank
From the center tank, then the outer cells, then inner cells
From the center tank, then from the inner cells to predetermined level, then outer cell fuel combines with inner cell fuel
In normal operation the cross feed valve is:
Closed for the take off
Automatically opened when the center tank has more than 100 kg fuel and either wing tanks has less than 5000 kg
Open for take off
Automatically opened by the MODE SEL push button switch
Are the engines still supplied in case of fuel filter CLOG:
Yes by using fuel coming from the IDG cooling and outer tank line
No
Yes, fuel bypassing the fuel filter (bypass valve)
What is the maximum total fuel capacity?
19,004 kg
20,829 kg
23,666 kg
How many channels is/are used in the Fuel Quantity Indications System?
3
2
1
Where is the vent surge tank located?
Outboard of each wing tank
In the wing tank
What are the minimum fuel quantity for the take off and maximum fuel quantity imbalance (heavier tank full) for take off or landing?
750 kg – 1200 kg
1500 kg – 1500 kg
2000 kg – 1500 kg
5000 kg – 1100 kg
What is the refueling time at nominal pressure (approx):
A. 20 minutes for all tanks
B. 17 minutes for wing tanks
C. 30 minutes for all tanks
A or b above
In case of single engine operation:
Cross feed valve must be kept open
Cross feed valve must be closed
The fuel of the opposite side of engine running is lost:
Cross feed valve is automatically kept opened
The fuel return valve is controlled by:
FMGC
FADEC
FLSCU
FQI
What does the FAULT light illuminated amber in the wing tank pb indicate?
Delivery pressure too high
Delivery pressure drops
The pb is in the OFF position
Why has a 2 % additional space been provided in each fuel tank?
For cooling purposes
For fuel expansion without spillage
The engine low pressure (LP) valve is closed by:
Engine fire pb or center tank transfer valve control logic
Engine fire pb or MODE SEL pb in manual
Engine fire pb or the engine MASTER SW
On the crossfeed pb, what is the meaning of the “ON” white light?
The valve opens
The valve is closed
The valve is fully open
At which fuel quantity is the low level “LO LVL” warning triggered on the ECAM?
Below 500 kg (1100 lb)
Above 900 kg (1980 lb)
Below 750 kg (1650 lb)
Below 250 kg (550 lb)
How can you check that fuel quantity (FQI) is in degraded mode?
FQ indication is boxed amber
FQ indication is dashed amber across the two last digits but it is impossible to determine which side is affected
FQ indication is dashed amber across the two last digits on the upper ECAM and ECAM fuel page must be called to check which tank is affected
FQ indication flashes on ECAM fuel page on the affected tank
When passing FL 200 gravity feeding occurs, what is the maximum flight level:
300 (FL 200 if jet B)
200 (FL 100 if jet B)
100
150 (FL 100 if jet B)
What is the purpose of the capacitance probes?
A. To measure the fuel level
B. To measure the fuel temperature
A and b above
When the wing tank pb is set OFF, the FAULT light is:
A. inhibited
B. Illuminated when delivery pressure drops
A or b above
Normal hydraulic power is provided by:
Engine driven pumps for all systems
Engine driven pumps for green and yellow, ELEC pump for the blue, ELEC pump for yellow (ground operation only)
Electric pumps for blue and yellow, engine driven pumps for green
Engine driven pumps for green and blue electric pump for yellow
The power transfer unit (PTU) is:
Reversible between green and yellow
One way between green and yellow
Reversible between all three systems
Reversible between blue and yellow
In flight, if Blue ELEC pump fails, Blue system:
A. Is lost
B. Can be recovered by RAT
C. Can be recovered by PTU
Both b and c
With both engines stopped, how is it possible to pressurize the Green system:
By the green engine pump
By the yellow engine pump and the PTU
By the yellow electric pump and the PTU
The RAT is automatically extended in case of:
Blue pump failure
Blue pump delivery pressure dropping below 1750 psi
Loss of (ENG. and APU) main generators
Can only be deployed manually
On ground the Blue system is pressurized when:
The APU is running
One engine is running
EXT power is available
Engine 2 energizes:
The blue system
The green system
The yellow system pump and the green system via the PTU should the green system pump fail
The yellow system comprises:
One engine driven pump, one electric pump, one hand pump
One engine driven pump, two electric pump
One engine driven pump, one hand pump and the RAT
The PTU runs automatically when delta P between the green and yellow system is more than 500 psi.
During green or yellow reservoir fluid low level
During green or yellow reservoir low air pressure
During green or yellow system low pressure
The priority valves operate in case of:
High hydraulic pressure in the green system
Low hydraulic pressure
High hydraulic pressure in the green and yellow system
The fire shut off valves shut off:
The blue and yellow systems
The yellow and green systems
The green and blue systems
In case of blue ELEC pump failure, when the RAT MAN ON pb (HYDRAULIC PANEL) is pressed:
The blue hydraulic system is pressurized by the RAT
The EMER GEN is supplying electrical system
The blue hydraulic system is pressurized and the EMER GEN is running
The hydraulic reservoirs are pressurized:
From the pneumatic system
From the Packs 1 and 2
From the LH ENG or the pneumatic system
In flight the ENG 1 pump FAULT light illuminates amber in case of: a reservoir low level, or a reservoir overheat, or reservoir low air press, or a pump low pressure
Yes
No
If on ground with ENG 1 stopped; does the ENG 1 pump FAULT light illuminate amber due to Green pump low pressure?
Yes
No
In case of reservoir overheat, the FAULT light of the faulty system stays on:
For 30 seconds
Continuously
As long as the overheat is detected
On ground and before engine start, with Blue pump pb in AUTO and AC power available, the Blue pump is:
Automatically energized
Energized when the Blue pump OVRD pb in the overhead maintenance panel is pressed
The Blue system includes operation of:
The flaps
The slats
The flats and the slats
The RAT, when extended in flight, pressurizes:
The green system
The yellow system and the green system via the PTU
The blue system
The Yellow system includes operation of:
The left and right elevator
The left elevator only
The right elevator only
The Yellow system may be powered by:
ENG 1 hydraulic pump
ENG 2 hydraulic pump or the Yellow electric pump or the PTU
ENG 2 hydraulic pump, the Yellow electric pump and the RAT
The Yellow system includes operation of:
The flaps
The flaps and slats
The slats
During the first engine start the PTU is
Automatically running
Tested
Inhibited
The RAT can be restowed:
In flight
On ground only
On ground and in flight
In flight the RAT is extended:
Manually only
Manually or automatically
Automatically only
In flight when the RAT is automatically extended:
The Blue hydraulic system is pressurized but the EMER GEN is not running
The Green hydraulic system is pressurized and the EMER GEN runs
The Blue hydraulic system is pressurized and the EMER GEN runs
Is it possible to interchange hydraulic fluid from Green to Yellow or Yellow to Green system:
No
Yes, thru the PTU
Yes, in case of leakage
The hydraulic fire shut off valve closes when:
The master switch is set to OFF
The Fire pb is released out
Automatically if the fire is detected
If the Green system is lost, slats operation is:
Normal
Slow
Lost
If the Green system is lost, flap operation is:
Slow
Normal
Lost
The Green system operates:
Spoilers 3
Spoilers 2 and 4
Spoilers 1 and 5
The Green system operates:
The right elevator
The left elevator
Both
The Green system operates:
The left aileron
The right aileron
Both
The Green system operates:
The Reverser 1
The Reverser 2
Both
The Yellow system operates:
The Reverser 1
The Reverser 2
Both
On ground, Blue ELEC pump pb at AUTO, the circuit is energized if:
One battery is on AUTO
Ground electrical power is ON
One engine is running or Blue pump OVRD pb on the overhead maintenance panel has been pressed
If Blue system is lost, the slats are:
Normal
Slow
Lost
If Blue system is lost, the flaps are:
Normal
Slow
Lost
The Blue system operates:
Spoilers 2 and 4
Spoilers 3
Spoilers 1 and 5
The RAT can be extended:
Automatically in case of loss of power to AC Bus 1 and AC Bus2
Manually from the overhead panel
Both
The Blue system operates:
The left aileron
The right aileron
Both
Can you operate a cargo door when no electrical power is available:
Yes, via a hand pump
No, no hand pump
Yellow ELEC pump pb switch OFF and cargo door manual selector valve set at open or close position, the PTU and the flight controls are:
Operative
Inhibited
If Yellow system is lost, the slats are:
Normal
Slow
Lost
If Yellow system is lost, the flaps are:
Normal
Slow
Lost
The ENG 2 fire valve is between the yellow reservoir and:
The ENG 2 hydraulic pump
The Yellow electric pump
The Yellow hand pump
The Yellow system operates:
The spoiler 3
The spoilers 2 and 4
The spoilers 1 and 5
In case of single hydraulic system low press:
The Master Warning light illuminates
The Master Caution light illuminates and the single chime sounds
There is no warning
In case of RSVR low air pressure, the hydraulic system affected is:
Definitely lost
May be recovered after descending to a lower altitude
With a single hydraulic system failure the flight control law is:
Normal
Alternate
Direct
With Green hydraulic system lost:
The landing gear extension is normal
The landing gear retraction is normal
The landing gear must be extended by gravity
With Green hydraulic system lost:
The NWS is lost
The NWS is operative
The NWS operates in alternate
With Green hydraulic system lost, the braking system is:
Normal
Alternate
Lost
With Green hydraulic system is lost, the anti skid is:
Lost
Limited to 2000 psi brake pressure
Operative on the Yellow hydraulic system
PTU at AUTO, the PTU automatically runs:
If the blue hydraulic system is lost
When differential pressure between Green and Yellow is more than 500 psi
As soon as a differential pressure between Green and Yellow system is detected
PTU running, the pressure delivered by the PTU is:
Stable at 3000 psi
Fluctuating between 2500 and 3000 psi
Hydraulic Green system only remaining the AP function is:
Available with AP 1
Lost
Available with AP 2
Hydraulic Green system only remaining, the horizontal stabilizer is:
Available
Lost
With Green and Yellow hydraulic systems lost, manual pitch trim is:
Available
Lost
Hydraulic Green system only remaining, the auto brake is:
Lost
Available
Alternate
With hydraulic Blue system only remaining:
The braking system is lost
Seven full brake applications are available via accumulator
The antiskid is still available
In flight, the Blue hydraulic system can be supplied by:
The RAT and the electrical pump
The engine driven pump
The PTU (power transfer unit)
It cannot be supplied
What happens when you set the wing anti-ice pb to ON, on the ground?
The wing anti-ice valves do not open
The wing anti-ice valves open for 30 seconds
The wing anti-ice valves remain open
The blue ON light illuminates on the wing anti-ice pb:
When the anti-ice valves open
When the pb switch is set to ON
When the FAULT light goes out
In case of loss of electrical power supply, the engine anti-ice valve:
Opens when the engine is stopped
Opens when the engine is running
Closes when the engine is running
Probe heating starts automatically when the switch is in AUTO position:
In low level after engine start and then normal power after lift off
Not heated on the ground, heats automatically at lift off
Operates in high heat after engine start
Operates in low heat until manually selected to high
In case of window heat computer failure, the other computer can replace the failed one:
Yes
No
Window heating comes on automatically when one engine is started:
Yes
No
The window heat computer provides two heating level for the wind shield:
High level when above 20,000 ft, Low level below 20,000 ft
High level in flight. Low level on ground
High level in icing conditions, Low level in other conditions
Pitot heating operates:
At low level on ground and normal power in flight
In flight only
On ground above 80 kts
Window heating can be selected ON manually at any time by the probe window heat pb:
Wrong
Right
Electrical heating is provided for the protection of:
Pitot and AOA
Pitot and TAT
Pitot, static ports, TAT, AOA
The engine nacelle is anti-iced by:
Air bleed from high pressure compressor
Air bleed from low pressure compressor
Electrically
When engine anti-ice valve is selected ON:
Continuous ignition is selected on
Continuous ignition is not selected on
The associated pack is closed
When an engine anti-ice valve is open:
The N2 of the associated engine decreases
N1 limit is automatically reduced and if necessary, the idle N1 is automatically increased for both engine in order to provide the required pressure.
N1 limit is automatically increased
The engine anti-ice valve closes in case of low air pressure:
Right
Wrong
How can you check the engine anti-ice has been selected:
With ON light on the associated Engine pb + ENG A-ICE on the ECAM Memo display
With ON light on the associated Engine pb + ENG A-ICE on the ECAM ENG page
The maximum speed to use the windshield wipers is:
200 kts
250 kts
230 kts
On a dry windshield, rain repellent system:
May be used as windshield washer
Must not be used
The rain repellent system is inhibited:
When both engines are shut down
On ground below 80 kts
Above FL 150
The rain repellent bottle should be replaced:
A. When the pressure indicator needle in the yellow sector
B. After each light
C. When refill float is in view on quantity indicator
A and C above
The electric wipers are controlled by 2 individual rotary selectors:
Yes
No
The wipers can operate at different speeds:
Low speed and high speed
Only one speed
Low, medium, high speed
The rain repellent bottle is located:
In the rear cockpit on the left side
In the avionic bay
In the cockpit on the right side
The timer supplies a measured quantity of rain repellent to the wind shield: to repeat the cycle the pb must be pressed again:
No
Yes
When not used, the wipers are out of view?
Right
Wrong
The wing anti-ice shut off valves close automatically in case of:
Engine failure
Loss of electrical power supply or leak detection
Cross bleed valve fault when wing anti-ice used
Slats protected by hot air supplied from the pneumatic system are:
Slats 1.2.4
Slats 2.3.4
The three outboard leading edge slats
The wing anti-ice shut off valves are controlled by:
1 wing anti-ice pb
2 wing anti-ice pbs
Automatically
Where do the wing anti-ice indications appear on the ECAM?
There is no indication on ECAM bleed page for wing anti-ice system
�ANTI-ICE” appears in white on the ECAM bleed page when the wing anti-ice pb is depressed
A green triangle appears in the ECAM Bleed page when the wing anti-ice pushbutton is depressed
The wing anti-ice pb switch ON light comes on:
When the anti-ice valves open
When the switch is set to ON
When the FAULT light goes off
The probe heating starts automatically when the pushbutton switch is in auto position:
Not heated on the ground, but heated automatically at lift off
Operates in high heat after engine start
Operates in low heat until manually selected to high
In low heat after engine start and then normal heat after lift off
Select the correct statement:
DMC 1 supplies data to PFD1-PFD2
DMC 1 supplies data to ND1-ND2
DMC 1 supplies data to PFD1-ND1-ECAM DUs
In case of PFDU failure, the PFD image is transferred to the NDU:
Manually
Automatically
Either manually or automatically
If the upper ECAM display is lost, the E/WD automatically transfers to lower ECAM display, if a system display is required:
It displays automatically
Press the RCL button
Switch off the corresponding ECAM display selector
Press and hold the relevant system pb
Which computer processes the red warnings:
SDAC
FWC
DMC
What is the basic role of the DMC's:
Acquire data from different sensors and computers and send it to the DUs
Generation of audio warnings
Generations of amber warnings
What is the meaning of the “INVALID DATA” message displayed in the DUs?
A. corresponding LCD is not energized
B. Electrical supply is good and corresponding DMC failed
As in answer b. Plus it is possible to get an image on again, by switching EIS DMC
Can you read amber warnings on FMA part of your PFD:
Yes
No
Do the “CHECK ATT” messages appear on both PFDs at the same time?
Yes
No
FAC's calculate speed trend and VLS. The extremities of the trend vector or VLS segment indicates: speed value at the next 10 sec. and 1.23 VS1G with present setting, is it correct
Yes
No
VLS indication is inhibited:
From touchdown until 10 sec. After lift-off.
With speed brakes extended
In both cases
FAC's compute VLS, F, S, shown on the PFD according to the position Flap Selector. Is above statement correct?
Yes
No
Altitude amber window appears, flashing:
When A/C goes below MDA
When A/C deviates from its selected altitude or selected FL
Both answers are correct
R.A. Gives height on PFD:
At the bottom of altitude sphere
On the altitude scale
Both indications
On the horizons line you find a cyan HDG or TRK symbol, is your FD pb switched ON?
Yes
No
When your FD bars flash for 10 sec. And then remain steady:
Reversion to the HDG V/S basic modes has occurred
ALT capture is active and you select another FL or at 1st AP or FD engagement
Loss of LOC or G/S in LAND mode or loss of LAND mode
All of the above is correct
During take-off, FMA show “SRS”, what is the order of horizontal FD bar:
Climb at V2 + 10 kt with both engines running
Climb at V2 with both engines running
TRK-FPA is the selected mode for AFS, the inertial FPV is normally on the horizon line. Can you see it in red colour:
Yes
No
The PFD displays Yaw Bar in green below 30 ft radio height , if localizer signal is available:
During TO (in RWY mode) or upon landing (in FLARE or ROLL OUT mode)
During TO or upon landing (in FLARE or ROLL OUT mode)
During TO (in RWY mode) only
All of the above is correct
Can you read optional data (WPT or VOR. D. NDB...), on rose VOR or rose ILS:
Yes
No
With radar selected on, what can you read on ND about antenna setting:
Tilt angle
Tilt angle + gain mode
What happens when ND shows red circle with “MAP NOT AVAIL” message:
MCDU failure
ADIRS not aligned, aircraft position delivered by FMGC is not valid
Engines not running
Landing gear can be extended by:
Green system or Yellow in stand by
Green system or mechanical gravity extension
Green system for unlocking, gravity extension and green system for downlocking
Blue system or mechanical gravity extension
The braking modes are:
Green with anti-skid, Yellow without anti-skid, Parking Brake
Green or Yellow with anti-skid, Yellow without anti-skid, Parking Brake
Green with or without anti-skid, Yellow without anti-skid, Parking Brake
The anti-skid and nose wheel switch is set off:
Anti-skid only is deactivated
Nose wheel steering only is deactivated
Anti-skid and nose wheel steering are deactivated
Anti-skid provides a fixed aircraft deceleration
L/G position is indicated by:
One panel on center instrument panel, one panel on overhead panel
ECAM only
One panel on center instrument panel and ECAM Wheel page
One panel on center instrument panel, ECAM, visual means on the wing
When auto brake operates, it can be disarmed by:
A. Pressing the pb or losing an arming condition
B. depressing 1 pedal if MAX , MED or LO autobrake mode is selected
C. Ground spoilers retraction
A or b or c
Maximum speed for landing gear retractions is:
200 kts
220 kts
250 kts
280 kts
The nose wheel steering is powered:
A. By hydraulic system
B. By electric system
A or b
Nose wheel steering is available when:
A. Gear doors open
B. Nose gear doors closed
Either a or b is correct
Nose wheel steering is powered by:
A. Yellow hydraulic system
B. Green hydraulic system
Either a or b is correct
When is pressure in the nose wheel steering system shut off:
With towing lever in towing position or both engines are shut down or aircraft in flight
During ground towing with one engine shut down or when aircraft speed is above 60 kts
The handwheel in the cockpit provide a wheel steering angle of:
85º
70º
75º
When both handwheel are operated simultaneously, the signals:
From the first pilot acting on his handwheel have priority
Coming from the captain have priority
Are added algebraically
Nose wheel steering by rudder pedals is limited to:
Up to 6º under all circumstances
Up to 6º depending on A/C speed
Handwheel and pedals are operated simultaneously:
Handwheel has priority
Pedals have priority (depending on speed)
Signals are mathematically added
Nose wheel steering is available:
A/C speed below 80 kts both ENG running, towing lever normal position, A/C on ground
A/C speed below 80 kts both ENG running, towing lever normal position, A/C on ground or in the air
A/C speed below 80 kts one ENG running, towing lever normal position, A/C on ground
Hydraulic pressure to the landing gear is supplied up to:
280 kts
Any speed
260 kts
After T/O the left main gear shock absorber remains in compressed position:
The gear can be retracted under all circumstances (safety)
The gear can be retracted provided the nose gear is centered
The gear cannot be retracted, gear lever is blocked
Is it possible (system wise) to lower the gear by gravity above 260 kts?
Yes
No
System page “WHEEL”: L/G position indicators (triangles), LH shows green triangles (gear down)? RH has no triangles are shown. The L/G is down and locked:
Yes
No
During an approach you get master warning and ECAM: “Gear Not Down!” The reason is:
A. L/G not down locked and Flaps at 3 or Full and both radio altimeters failed.
B. L/G not down locked, Flaps at 3 and radio height above 750 ft
A or b
The brakes are actuated by two independent systems, pressurized by the:
Blue and Green hydraulic system
Yellow and Green hydraulic system
Blue and Yellow hydraulic system
The alternate brake system uses:
A. The yellow hydraulic system
B. The hydraulic accumulator
A + b
Brake pressure from the hydraulic accumulator is still available:
In normal (with anti-skid)
In alternate (with anti-skid)
In alternate (without anti-skid)
The anti-skid system gets its references speed from:
ADIRU 1
ADIRU 1 or 2
ADIRU 1, 2 0r 3
The principle of anti-skid is:
Comparing the speed difference between the four wheels
Comparing wheel speed with A/C reference speed
Comparing wheel speeds between left and right landing gear
Following ADIRS 1 and ADIRS 3 failure, is the anti-skid still available?
Yes
No
Green hydraulic system available, you find the A/SKID and N/W STG sw in OFF position:
Braking is normal, nosewheel steering lost
Braking is alternate, nosewheel steering normal
Braking is alternate, nosewheel steering lost
Alternate braking using the yellow system. Autobrake is:
Still available with anti-skid
Lost
Still available without anti-skid
Setting the parking brake deactivates all braking modes, except the anti-skid:
True
False
Setting the parking brake ON deactivates the auto brake:
True
False
Auto Braking is initiated by:
A. Reverse thrust selection
B. Ground spoilers extension
A + b
After landing you retract the ground spoilers by bringing thrust levers from reverse to idle. The auto brake is now disarmed:
Yes
No
The brake and accumulator pressure gauge shows pressure:
From yellow hydraulic system
From accumulator only
From both yellow brake system and brake accumulator
MAX braking has been selected: take off being aborted, engines in reverse, you have forgotten to arm the ground spoilers, is autobrake activated:
Yes
No
The HOT light on the BRK FAN pb illuminates when brake temperature reaches:
250ºC
300ºC
315ºC
On WHEEL page of ECAM, AUTO BRK is flashing green:
Auto brake is disengaged
Auto brake failure
Anti-skid failure
On WHEEL page of ECAM, a green arc appears on one wheel indicator meaning the brake temperature is above:
300ºC
100ºC
50ºC
After lift off, is brakes HOT warning on ECAM still available:
Yes, gear down or up
Yes, gear down only
Not
On the RAMP with the APU running, PB is set ON. Message on ECAM shows PARK BRK:
In green
Not at all
In yellow (because of ACCU press)
After a landing gear gravity extension, is it possible to restore normal landing gear operation if green hydraulic pressure is available:
Yes
No
The landing gear indicator panel receives the information from microswitches and proximity detectors connected to:
LGCIU 1
LGCIU 2
Both
The red arrow, near the landing gear lever illuminates when:
Landing gear is not down locked in landing config.
Landing gear is not uplocked after retraction
Landing gear is in abnormal position
LDG Gear indicator panel UNLK LT illuminates red if:
Gear is not locked in the selected position
Gear is extended by gravity and doors are not closed
Gear is extended normally and doors are not closed
The MAX speed with landing gear extended (VLE) is:
300 kts/ M..70
280 kts/ M..67
260 kts/ M..60
The MAX speed at which the landing gear may be extended is:
260 kts
250 kts
240 kts
Which ADIRS's close the safety valve of the green hydraulic supply when speed > 260 kts:
ADIRS 1 and 2
ADIRS 1 and 3
ADIRS 2 and 3
What is the MAX tire speed:
205 kts
195 kts
185 kts
Are there any mechanical visual gear down lock indicators:
Yes
No
How many turns are necessary to extend the landing gear by gravity using the handcrank:
Ten turns clockwise
Five turns clockwise
Three turns clockwise
The braking systems are:
Green with anti-skid, yellow without anti-skid, parking brake
Green or yellow with anti-skid, yellow without anti-skid, parking brake
Green with or without anti-skid, yellow without anti-skid, parking brake
In flight, with the parking brake set to ON, a message on ECAM shows PARK BRK:
In green
In amber
In blue
When the autobrake operates, it can be disarmed by:
A. Ground spoilers retraction
B. Pressing the Mode pb or losing an arming condition
C. Action on 1 pedal in LO, MED or MAX Mode
Any: a, b or c
What happens when the mask is used with the selector at 100% position?
Mask is supplied with diluted oxygen on demand
Mask is supplied with undiluted oxygen on demand
Mask is supplied with undiluted oxygen continuous flow
A thermal discharge of the crew oxygen bottle is indicated by:
�Thermal discharge” message on ECAM
Green blow out disc missing
Red blow out disc missing
No indication of thermal discharge provided
In the passengers oxygen system, a generator, once activated, delivers oxygen for:
5 minutes, if all masks are used
30 minutes, if only one mask is in use
15 minutes same distribution to each mask
If in the cockpit the master selector of the EVAC command panel is in “CAPT” position and purser presses his EVAC “COMD” pb, what will happen?
EVAC signals are energized in the cabin only
All EVAC signals are energized
EVAC signals are energized in the cockpit only
If cabin altitude rises above 14,000 FT, Oxygen masks will drop out:
Only by actuation of a switch on the Captain Panel
Automatically by cabin pressure and/or cabin attendant action
Automatically by cabin pressure and/or flight deck action
The captain may call all cabin attendants at the same time:
True
False
Where are the EVAC signals located?
In the cockpit and next to forward left and aft left cabin door
In the cockpit and next to each cabin door
In the cockpit and next to each cabin door and emergency overwing exit
State the location of the “EVAC COMMAND” switch:
Purser station and C/A aft left
Purser station and pilot overhead panel
Pilot overhead panel and all C/A station
How many escape ropes are in the cockpit?
2 escape ropes – 1 over each window they can be used through the left or right window
2 escape ropes – each of them must be used through the window to which it corresponds
3 escape ropes for the 2 cockpit crew members. The extra one is to be used by some particularly big people
With engines and APU running and APU bleed valve selected ON, select the correct statement:
Engine bleed valves open, X bleed valve opens, APU bleed valve closes
Engine bleed valves close, X bleed valve opens, APU bleed valve opens
Engine bleed valves open, X bleed valve closes, APU bleed valve opens
Engine bleed valves close, X bleed valve closes, APU bleed valve opens
To provide external air for ENG start the following switching is required:
Pneumatic X-bleed AUTO
Pneumatic X-bleed OPEN
Engine bleed switches OFF
APU bleed switch OFF
Air bleed from the engines is:
Not cooled prior to being used by the systems
Cooled in a heat exchanger by cooling air bleed from fan section
Cooled using ambient air
Only cooled in air conditioning part
High pressure air is supplied from:
Engine 1 and 2 bleed systems, APU load compressor, HP ground connection
Engine 1 and 2 bleed systems
Engine 1 and 2 bleed systems and APU load compressor
Pneumatic system operation is controlled and monitored by:
One bleed monitoring computer
Two bleed valve computers
Two bleed monitoring computers
Which source operates the bleed valve?
Pneumatic
Electric
Both
What happens when pressure and temperature are not sufficient to supply the corresponding engine bleed valve:
IP valve closed
HP valve opened, IP stage closed
HP valve opened, IP stage remains in the same configuration
Can you control the HP valve position through the air bleed cockpit panel?
Yes
No
If the bleed valve closes, the HP valve:
Opens automatically
Closes automatically
Temperature regulation is achieved by the precooler which regulates and limits the temperature at:
150ºC
85ºC
200ºC
Which source controls the crossbleed valve:
Pneumatic
Electric
Cross-bleed valve is provided with 2 electrical motors:
One for the automatic mode, the other one for the manual mode
Two for the automatic mode
Two for the manual mode
In case of low upstream pressure, the high pressure valve (HP valve) is:
Pneumatically closed
Open
Electrically opened
Electrically closed
On ground the start sequence is automatically aborted:
There is no automatic abort sequence
Only in case of hot start or hung start
Only in case of no light up
In case of hot start, hung start, stall or no light up
During an automatic start on ground, the sequence is:
Ignition by N2 > 16%, HP fuel valve opening by N2 > 22% ; start valve closure by N2>50%
Ignition and HP fuel valve opening by N2 > 16% - start valve closure by N2 > 50%
Ignition and HP fuel valve opening by N2 22% - start valve closure by N2 > 50%
Ignition by N2 > 16% - HP fuel valve opening by N2 > 22% - start valve closure by setting mode selector to NORM
Thrust reversers are actuated by:
Hydraulic actuators: green for engine 1 – yellow for engine 2
Hydraulic actuators: green for both engines
Hydraulic actuators: blue for engine 1, yellow for engine 2
Pneumatic actuators
The FADEC is electrically supplied by:
Aircraft electrical system only
Batteries if A/C electrical power fails
Self powered above 12% N2
Aircraft electrical system or self powered in an emergency
In manual mode, when the thrust levers are between the CLB detent and IDLE:
Each position of the levers corresponds to an N1
N1 is climb N1
N1 is idle N1
N1 is frozen
What is the EGT limit at TOGA power setting:
890ºC on 1 Engine or 850ºC both engines running
790ºC during 5 min. (1 min. on 1 engine)
950ºC during 5 min. (10 min. on 1 engine)
What is the maximum continuous oil temperature:
150ºC
140ºC
155ºC
The max continuous oil temp. Limit maybe exceeded, what is the limit, and under what conditions?
155ºC for less than 15 min.
155ºC for less than 15 min.if one engine is failed
The max cont. Oil temp.must not be exceeded
What is the minimum starting oil temperature:
-40ºC
-10ºC
0º
What is the minimum oil quantity (ECAM indications):
5 qts + estimated consumption (0.6 qt/hr)
11 qts + estimated consumption (0.6 qt/hr)
9.5 qts + estimated consumption (0.5 qt/hr)
What is the minimum oil pressure at ground idle:
13 psi
10 psi
Variable with oil temperature
What is the maximum N1:
105%
104%
100%
What is the maximum N2:
105%
102%
100%
What is the maximum N2 for starter engagement:
0%
25%
20%
What is the maximum starter operating time: (4 consecutive cycles of)
8 min. Followed by 15 min. Of no operation
5 min. Followed by 20 sec. Of no operation
2 min. Followed by 20 sec. Of no operation
Starter cooling time requirements are:
15 min. Cooling time after 4 cycles of 2 min.
5 min. Cooling time after 4 cycles of 2 min.
2 min. Cooling time after 4 cycles of 8 min.
The maximum reverse thrust may be used down to:
A/C stop according to EGT limit
70 knots (idle reverse down to A/C stop)
40 knots (idle reverse down to A/C stop)
What is the maximum allowable FLEX TEMP?
ISA + 29ºC
ISA + 53ºC
ISA + 46ºC
Reduced thrust is permitted:
If outside air temp. Is higher than corrected temp.
On contaminated runway or with one (or more) reverser inop.
If corrected temp. Is lower than Tmax FLEX (ISA + 53ºC)
In manual thrust, in cruise, the pilot should limit the N1. What is the limit?
Displayed MAX CLB N1, minus 2.4 %
Displayed MAX CLB N1, minus 1.9 %
Displayed MCT N1
Is the MAX CRUISE N1 displayed on upper ECAM:
No
Yes
At Toulouse (500 ft): Tref is 29ºC, outside air temp. is 36ºC and you found a corrected flex temp of 33ºC. Is it possible to use FLEX thrust for take-off?
Yes
No
EGT indication becomes red on E/W display when EGT is higher than:
855ºC
890ºC
950ºC
What is the FADEC:
An engine control box
A thrust control unit controlling each engine.
Is a digital engine control system that performs complete engine management.
The FADEC system is:
Always powered by AC electrical circuit
Self powered
Self powered above 12% N2 with AC power when N2 is below 12%
What device provides direct closure of the HP shut-off valve?
The master switch at OFF position
The ECU
HMU
Which valve ensures an adequate fuel flow:
The HP fuel SOV
The BSV (burner staging valve)
The fuel metering valve of the HMU
Is the engine still supplied in case of fuel filter CLOG?
Yes, by using the fuel coming from the IDG cooling tank line
Yes, by by-passing the fuel filter (by-pass) valve)
No, the engine stops
Cranking may be manually selected by setting:
The MODE selector to CRANK and the Master Sw. to ON
With Master Sw. to OFF, the MODE selector to CRANK and MAN START pb to ON
Same as b. with Master Sw. ON
During an automatic starting sequence, the pack valves close when:
IGN/START is selected
APU bleed is selected to ON and IGN/START is selected
The Master Sw. Is selected ON with IGN/START selected
During an automatic starting sequence:
Start valve closes at N2>43%
Start valve closes at N2>45%
Start valve closes at N2>50%
Maximum EGT during engine starts is:
855ºC
890ºC
725ºC
The FADEC automatically selects continuous ignition in the following cases:
Wing anti-ice ON or engine flame out.
Ignition delay during start, flameout detected or EIU failure while engine running.
Flame out detected, EIU failure while engine running or ENG anti-ice ON.
How is the oil cooled?
By the engine fuel/oil heat exchanger and the servo fuel heater
By oil recirculation
By the air/oil heat exchanger
Oil pressure indicator becomes red when pressure is lower than:
16 psi
200 psi
13 psi
In A/THR Mode the thrust computed by the FMGC is limited:
By the ECU (with the TLA)
By the mode engaged on the FCU
By the FMGC itself
The thrust reverser activation condition are:
Aircraft on the ground and thrust lever between reverse idle detent and max reverse
Spoiler armed and thrust levers on the reverse sector
Thrust levers in full reverse sector
REV green appears on the N1 indicator when:
Thrust levers are selected to full reverse sector
The reverse doors are fully deployed
The thrust lever position is in the idle reverse sector
Reverse deployment requires TLA – 3º, signal from the SEC's. One reverse will be lost if:
A. SEC's 1 + 2 are lost
B. SEC's 1 + 3 are lost
A or b
The low pressure rotor (N1) consist of:
A front Fan – 2 stage booster – 5 stage LP turbine
A front Fan (1 stage) – 4 stage booster – 4 stage LP turbine
A/THR can be engaged:
Manually on ground (ENG. Running), automatically after take-off
In flight, manually or automatically if there is an alpha floor detection
Automatically when pilot initiates a take-off or a go-around or if there is an alpha floor detection after T/O and down to 100ft (RA) on landing
In flight, if the instinctive disconnect pb is pressed for more than 15 sec., the A/THR including alpha floor is definitely lost:
Right
Wrong
At take-off, as soon as the power is set (FLEX or TOGA):
ATS function is engaged provided A/THR pb on FCU is pressed in
ATS function is active
ATS function is engaged but not active
After a FLEX TO, you have an engine failure and you want to select MCT:
You have the throttle lever in FLEX/MCT: MCT selection is automatic
You set the throttle levers out of the FLEX/MCT detent (to TOGA or CLB detent) then back to FLEX/MCT position
Pressing the ENG. FIRE pb switch (on the ENG fire panel) causes the closure of:
Fuel LP valve
Fuel LP valve and HP valve (due to LP valve closure)
Fuel HP valve
ASYM amber message (FMA) means:
One thrust lever is set out of climb notch (both engines running)
Asymmetric power is established due to FADEC malfunction
Asymmetric power is established due to TLA resolver fault
MCT amber message (in the left part of the FMA) means:
Throttles are not in MCT position after engine failure in flight
Throttles are not in MCT position after engine failure when speed is > green dot (VFTO)
�LVR CLB” flashes white on FMA, if the throttles are not in CL position when:
The A/C is above the altitude of thrust reduction
The A/C is at lift-off
The landing gear is retracted
The thrust limit is computed by:
The FMGC according to the AP/FD mode
The ECU according to the thrust lever position
The ECU according to the AP/FD mode
The FMGC according to the ECU order
On ground the automatic start sequence is:
Start valve and LP fuel valve opens, ignition starts when N2 > 16%, HP fuel valves open when N2 > 22% when N2 > 50%, start valve closes and igniter off
Start valve opens, ignition starts when N2 > 16% when N2 > 50% start valve closes and igniter off
Start valve and HP fuel open when N2 > 22%, start valve closes when N2 > 50%
Start valve opens, ignition starts when N2 > 16% LP and HP fuel valves open when N2 >22%. When Eng Mode Sel. Set to NORM, start valve closes and igniter off
The fasten seat belt, no smoking and exit signs illuminate:
The appropriate switches are ON and/ or excessive cabin altitude is detected
The appropriate switches are OFF and/ or excessive cabin altitude is detected
All of the above
With the switch in the arm position, emergency lighting is provided when:
AC bus 2 fails
AC Essential Bus fails
AC Bus 1 or DC Shed Essential Bus fails
DC Bus fails
The cockpit door:
Normally open into the cabin
Normally opens into the cockpit but a mechanical override enables the flight crew to open the door from the cabin side.
Normally opens into the cockpit but a mechanical override enables the flight crew to open the door from the cockpit side.
The aircraft is fitted with emergency evacuation slides at:
The 4 entry doors
The overwing exits
The 4 entry doors and the overwing exits
If a slide fails to inflate automatically:
A. It cannot be inflated
B. It must be inflated by manual activation
C. It may be used as a manually held escape slide
B + c
When opened in an emergency the passenger entry doors:
Are pneumatically assisted into the open position
Will need 2 flight attendants to push them open
Are assisted to the open position by slide inflation
Evacuation command button at the forward flight attendant position:
Can only be activated, provided the cockpit switch at the CAPT and PURS position
Can be activated at any time
Can only be activated on ground
Overrides all other signals
Emergency lighting using the integral batteries will provide lighting for:
30 minutes
24 minutes
60 minutes
12 minutes
Is the alert active when the command pb. On the EVAC purser panel is pressed?
Yes, at any time
Yes, but only on the ground
Yes, provided the cockpit EVAC switch in the CAPT and PURS position
Yes, it overrides all other signals
At the gate, a red light flashes under the door window when:
Slide is armed and engines are running
Engines are stopped, slide is disarmed and cabin is pressurized
Engines are running and slide is disarmed
How many escape ropes are in the cockpit?
2 escape ropes – 1 over each window, they can be used through the left or right window
2 escape ropes – each of them must be used through the window to which it corresponds
3 escape ropes for the 2 cockpit crew members, the extra one is to be used by some particularly big people
Where are the EMER EVAC command pb. Switches installed?
In the cockpit and next to each cabin door
In the cockpit overhead panel only
On the overhead panel and the Fwd/Aft Attendant Panels
Smoke detection systems are installed in:
A. Avionics bay and cargo compartment
B. Avionics bay, cargo compartment and lavatories
As in b., plus the galleys
With “AVNCS SMOKE” warning activated the amber “SMOKE” light illuminates associated with the:
BUS TIE pb
GEN 1 pb
GEN 1 LINE pb
The avionics bay smoke detector is located in the:
Avionics bay
Ventilation extract duct
Skin heat exchanger
With the BLOWER + EXTRAC pbs in OVRD the ventilation gets air from the:
Inlet valve
Skin heat exchanger by-pass valve
Air conditioning inlet valve
Avionic smoke warning is inhibited during take-off from:
80 kts to lift-off
80 kts to 1500 ft
Not inhibited
Lavatory smoke detectors are situated in each lavatory air extraction duct:
True
False
At activation of “LAVATORY SMOKE” warning the fire extinguishing system is automatically discharged:
True
False
Lavatory smoke detectors send warnings to:
ECAM and Nose interphone panel
ECAM and CIDS
ECAM, CIDS and Nose interphone panel
Smoke detection in FWD and AFT cargo compartment is consists of:
2 smoke detectors and a SDCU
2 smoke detectors in FWD Bay, 4 detectors in AFT Bay and SDCU
4 smoke detectors in each bay and a SDCU
Air conditioning smoke warning is activated if smoke is detected in the:
Air conditioning duct
Hot air manifold
Pack outlet ducts
No warning system is installed
In case of cargo compartment smoke warning, the agent bottle if discharged should be empty in less than:
10 seconds
3 minutes
1 minute
When pressing the CARGO SMOKE Test pb for at least 3 seconds, the smoke detectors are tested by SDCU, the RED smoke light comes on twice associated with ECAM and the isolation valves close:
True
False
{"name":"A320 TKE (CAAP)", "url":"https://www.supersurvey.com/QPREVIEW","txt":"Test your knowledge on the A320's Air Conditioning system with this comprehensive quiz! Designed for aviation enthusiasts, students, and professionals, it covers critical aspects of the air conditioning and avionics ventilation systems.Prepare yourself for challenges like:Detailed multiple-choice questionsUnderstanding pack flow and temperature controlIdentifying the roles of key components","img":"https:/images/course2.png"}
More Quizzes
Jet Systems Knowledge Quiz
10579
AVIONICS REVIEW
301532
Test
210
Kuis Tentang Berbagi
1780
Free Civil Aviation Regulations Knowledge Test
201023344
Free CCMA Practice Test - Boost Your Exam Confidence
201023916
CRCST Certification: Ace Your Sterile Processing Skills
201074277
Ultimate Star Wars Ship: Which Galactic Vessel Are You?
201023916
Painter Of The Night: Which Character Are You?
201026108
Clouds and Climate
15827971
Test Your Knowledge: Questions About Sickle Cell Disease
201032068
Harriet Tubman Questions: Test Your Knowledge
201029852